Direct-On-Line (DOL) Starter:
In the realm of electrical engineering, motor starters play a vital role in initiating and controlling the operation of electric motors. Among the various types of motor starters, the Direct-On-Line (DOL) starter is one of the simplest and most commonly used configurations. In this blog, we will delve into the uses, merits, and demerits of DOL starters, exploring why they are employed and where they are rated for motors.
What is a DOL Starter?
A Direct-On-Line (DOL) starter is an electromechanical device that provides a simple and cost-effective means to start electric motors. As its name suggests, a DOL starter directly connects the motor to the power supply, providing full voltage at the start, without any initial voltage or current regulation. The starter comprises a contactor, an overload relay, and various control devices for motor protection.
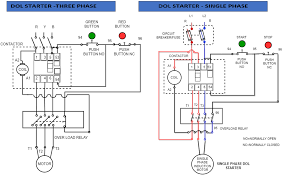
Components of a DOL Starter:
Contactor: A contactor is an electromagnetic switch that controls the electrical connection between the motor and the power supply. It consists of a coil, movable contacts, and stationary contacts.
Overload Relay: The overload relay is a protective device that senses the current flowing through the motor and protects it from damage caused by excessive current. It is connected in series with the motor.
Working Principle:
Starting Process: When the start button is pressed, the control circuit sends a signal to energize the coil of the contactor. The energized coil generates a magnetic field, attracting the movable contacts and closing the circuit between the power supply and the motor.
Full Voltage Application: As the circuit closes, the full line voltage is directly applied to the motor windings, causing a high inrush current. This results in a rapid acceleration of the motor’s rotor, initiating its rotation.
Running State: Once the motor reaches its full speed, the operator releases the start button. The contactor’s coil remains energized by a separate holding circuit, keeping the contactor’s contacts closed and maintaining the connection between the power supply and the motor.
Overload Protection: The overload relay, connected in series with the motor, continuously monitors the current passing through the motor windings. If the current exceeds a preset threshold due to an overload or fault, the overload relay trips, opening the circuit and disconnecting the motor from the power supply. This protects the motor from overheating or damage.
Stopping the Motor: To stop the motor, the operator presses the stop button, which breaks the circuit in the control circuit. This de-energizes the contactor’s coil, releasing the movable contacts and opening the circuit between the power supply and the motor.
Advantages of a DOL Starter:
Simplicity: DOL starters have a straightforward design and are easy to understand, install, and maintain.
Cost-Effective: Due to their simplicity, DOL starters are cost-effective compared to other motor starter configurations.
Disadvantages of a DOL Starter:
High Inrush Current: The direct connection to the power supply results in a high inrush current during startup, which can cause voltage drops and potential damage to the motor windings.
Mechanical Stress: The instantaneous application of full voltage can lead to mechanical stress on the motor and connected mechanical systems.
Limited Starting Torque Control: DOL starters lack the ability to control or limit the starting torque, which can be a limitation in certain applications.
Components of a DOL Starter:
Contactor: A contactor is an electromagnetic switch that controls the electrical connection between the motor and the power supply. It consists of a coil, movable contacts, and stationary contacts.
Overload Relay: The overload relay is a protective device that senses the current flowing through the motor and protects it from damage caused by excessive current. It is connected in series with the motor.
Working Principle:
Starting Process: When the start button is pressed, the control circuit sends a signal to energize the coil of the contactor. The energized coil generates a magnetic field, attracting the movable contacts and closing the circuit between the power supply and the motor.
Full Voltage Application: As the circuit closes, the full line voltage is directly applied to the motor windings, causing a high inrush current. This results in a rapid acceleration of the motor’s rotor, initiating its rotation.
Running State: Once the motor reaches its full speed, the operator releases the start button. The contactor’s coil remains energized by a separate holding circuit, keeping the contactor’s contacts closed and maintaining the connection between the power supply and the motor.
Overload Protection: The overload relay, connected in series with the motor, continuously monitors the current passing through the motor windings. If the current exceeds a preset threshold due to an overload or fault, the overload relay trips, opening the circuit and disconnecting the motor from the power supply. This protects the motor from overheating or damage.
Stopping the Motor: To stop the motor, the operator presses the stop button, which breaks the circuit in the control circuit. This de-energizes the contactor’s coil, releasing the movable contacts and opening the circuit between the power supply and the motor.
Advantages of a DOL Starter:
Simplicity: DOL starters have a straightforward design and are easy to understand, install, and maintain.
Cost-Effective: Due to their simplicity, DOL starters are cost-effective compared to other motor starter configurations.
Disadvantages of a DOL Starter:
High Inrush Current: The direct connection to the power supply results in a high inrush current during startup, which can cause voltage drops and potential damage to the motor windings.
Mechanical Stress: The instantaneous application of full voltage can lead to mechanical stress on the motor and connected mechanical systems.
Limited Starting Torque Control: DOL starters lack the ability to control or limit the starting torque, which can be a limitation in certain applications.
Rating of DOL Starters:
DOL starters are rated based on the motor’s power rating (in kilowatts or horsepower) and the voltage and frequency of the power supply. When selecting a DOL starter, it is crucial to ensure compatibility with the motor’s power rating and consider any specific environmental conditions or regulatory requirements.
Direct-On-Line (DOL) starters offer a simple and cost-effective solution for starting small induction motors with relatively low starting torque requirements. Their merits lie in their simplicity, high starting torque, and quick motor response. However, the high inrush current, mechanical stress, and limited starting torque control are important factors to consider. When selecting a motor starter, it is crucial to evaluate the specific application requirements and consider alternative starter types for cases where smoother acceleration or torque control is necessary.
Few Questions
Q1: What does DOL stand for in DOL starter? A1: DOL stands for Direct-On-Line in DOL starter.
Q2: What is the purpose of a DOL starter? A2: The purpose of a DOL starter is to provide a simple and direct means of starting electric motors.
Q3: How does a DOL starter provide starting torque to the motor? A3: A DOL starter provides starting torque by applying full voltage directly to the motor windings.
Q4: What is the main advantage of a DOL starter? A4: The main advantage of a DOL starter is its simplicity and cost-effectiveness.
Q5: What is the function of the contactor in a DOL starter? A5: The contactor in a DOL starter is an electromagnetic switch that controls the electrical connection between the motor and the power supply.
Q6: How does a DOL starter protect the motor from excessive current? A6: A DOL starter protects the motor from excessive current through an overload relay that trips and opens the circuit if the current exceeds a preset threshold.
Q7: Can a DOL starter control the starting torque of the motor? A7: No, a DOL starter does not have the capability to control or limit the starting torque of the motor.
Q8: What are the potential drawbacks of a DOL starter? A8: Drawbacks of a DOL starter include high inrush current during startup and limited control over starting torque.
Q9: Where are DOL starters commonly used? A9: DOL starters are commonly used in applications involving small induction motors, such as fans, pumps, compressors, and conveyor systems.
Q10: Is a DOL starter suitable for applications that require smooth acceleration? A10: No, a DOL starter is not suitable for applications that require smooth acceleration. Alternative starter types like star-delta or soft starters are preferred in such cases.
Maintenance Of Equipments
Now, let’s talk about the Preventive maintenance of the following equipment.
- Transformer Preventive Maintenance.
- Street Light Preventive Maintenance.
- AC Maintenance.
- DG Set Maintenance.
- Preventive Maintenance of ACB.
- Preventive Maintenance of Capacitor Bank.
- Preventive Maintenance of Lifts.
- Preventive Maintenance of Earthing.
- Preventive Maintenance of Ceiling Fans.
- Preventive Maintenance of Power Panels.
- Preventive Maintenance of Circuit Breakers.